One of the world’s leading manufacturers of the plastic polyurethane (PUR) is Hennecke GmbH in Sankt Augustin near Bonn in North Rhine-Westphalia.
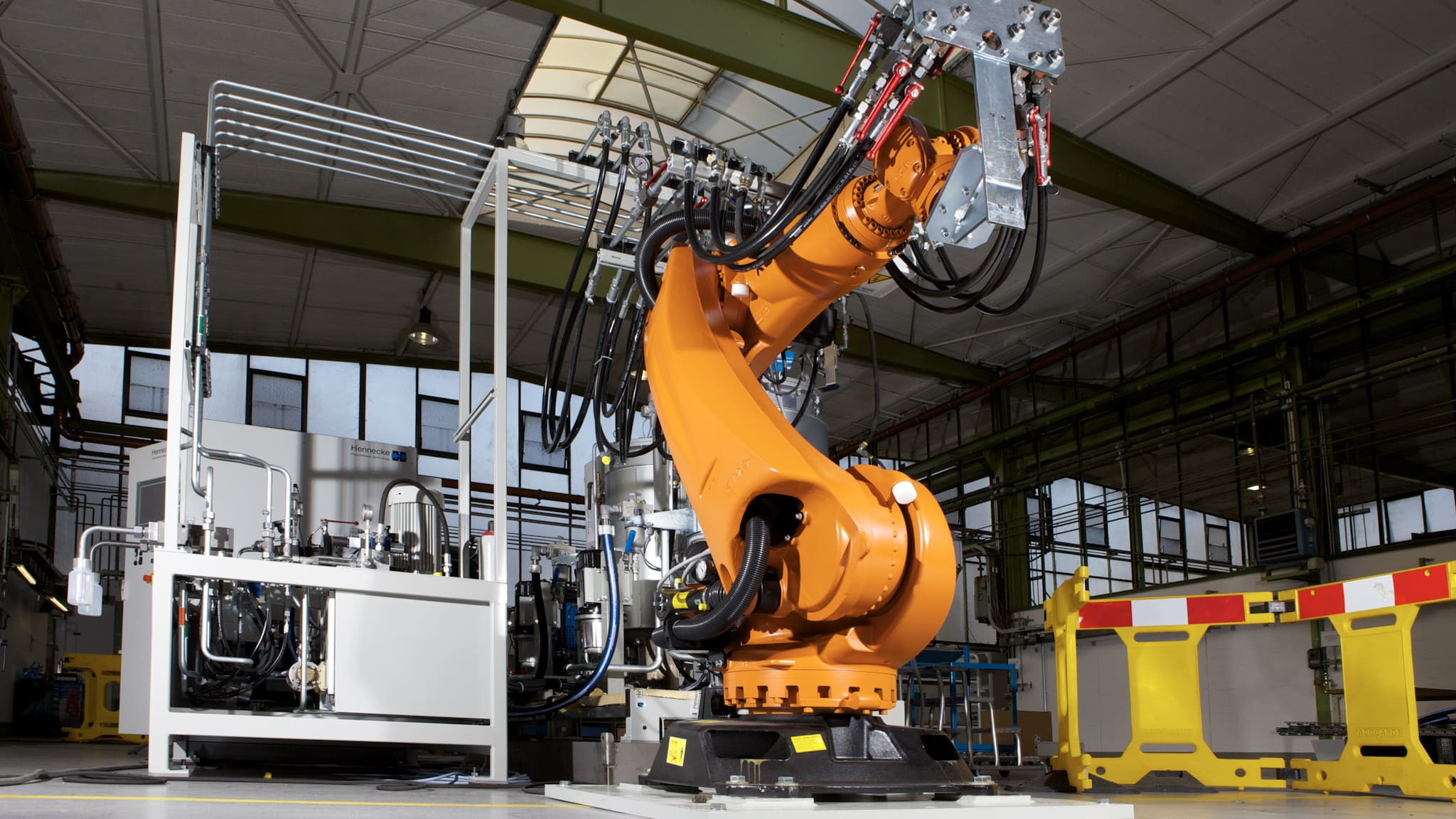
05.06.2012
Versatility PURe and simple
One of the world’s leading manufacturers of the plastic polyurethane (PUR) is Hennecke GmbH in Sankt Augustin near Bonn in North Rhine-Westphalia. What seems almost unpronounceable is nevertheless known to all of us.
Application fields
Every one of us has held something made of PUR at some time. For example, your car’s steering wheel, a football, wellington boots or a mattress are just a few examples of the possible uses of this multi-faceted plastic in our everyday lives. Do-it-yourselfers and craftsmen know PUR as a construction foam. But the experts draw a clear distinction between soft foam and hard foam products. In the industry, hard polyurethane foam is often used as a insulating and damping material in “sandwich” constructions. These elements consist of inner and outer metal composites. The space between them is filled with PUR foam, which expands during the reaction. With its excellent insulating properties, PUR is the ideal substance for significantly improving the energy balances in buildings, for example. The contribution PUR has been making to the reduction of climate gas emissions for years should not be underestimated. For example, the PENTANE PROCESS TECHNOLOGY (PPT) from Hennecke replaced the greenhouse gas CFC in refrigerators, and is one of the primary reasons why there are now refrigerators with energy class A++. Although polyurethanes are manufactured from a petroleum base, they are endowed with such exceptional product properties that they help to conserve many other resources. For instance, heating and cooling needs are reduced by the insulating characteristics mentioned previously. This lowers CO2 emissions. PUR is the most commonly used plastic in the car building industry, and is indispensable for improving comfort and texture in an enormous variety of applications. PUR is also major factor in automotive applications where weight reduction is important, because less weight means less fuel consumption. And to top it all off, PUR is recyclable and can be processed to make new products.
Over 60 years’ experience
The machinery, equipment and systems manufactured by the Hennecke Group offer solutions for all of the core technologies associated with all aspects of processing PUR. In this business, Hennecke can draw on over 60 years of experience. Since it was founded in 1945, this highly respected company based in Sankt Augustin has been highly instrumental in driving advances in the PUR industry, and has received many patents in the field. As early as the 1950s, Hennecke developed the first system in the world for mixing the components of PUR, polyol and polyisocyanate, under high pressure. This has served as the foundation for high product quality and efficient use of raw materials. Today, Hennecke employs about 450 staff worldwide and is indisputably a market leader in its segment. The global posture of the company and its expert consultants and service technicians in all major economic regions of the world have earned Hennecke a reputation as a reliable partner in many joint international undertakings. The plant manufacturer sets aside a substantial budget for research and development every year, and so is able to offer innovative technologies with outstanding economic and ecological benefits. With its subsidiaries in Pittsburgh/USA, Shanghai/China, Aichi/Japan, and Singapore, and through a network of local agencies, the group offers its customers 360° service with a truly global reach. This begins with the rapid delivery of original spare parts and encompasses every aspect up to and including practice-based training courses.
Products for every application
With its products, Hennecke GmbH offers its customers equipment with which any kind of PUR can be produced. The machinery and plant spectrum ranges from largely standardised machines for newcomers to the industry, to well-established high-tech systems and custom-designed and built production machinery for every conceivable field of application. The heart of every polyurethane plant is the metering unit. The unit is driven by high pressure metering machines with piston pumps or metering pistons depending on the specific application. One of the most important components of the metering machine itself is the mixhead. Most of the Hennecke portfolio of mixheads operates in high pressure processes and converts pressure energy into mixing energy. This ensures optimum mixing behaviour and a homogeneous PUR output. This technology is highly complex and relies on components of immense durability. No less is true of the media and hydraulic hoses, which Hennecke began purchasing from HANSA‑FLEX in 2011. “We recognised certain synergies very quickly, and we see the potential for further cooperation”, declares Jürgen Ternes, strategic buyer for Hennecke. Accordingly, the first metal hose lines and cylinders have already been supplied by HANSA‑FLEX specialist operations. Further options and solutions for developing this cooperation are currently under discussion.
The total package is a winner
“HANSA‑FLEX convinced us with quality, fast delivery times, flexibility, and its extensive branch network,” said Jürgen Ternes in an interview. “For example, we have a customer number that is recognisable in every branch anywhere in the world.” Not everyone can offer that. In addition, HANSA‑FLEX provides consulting services that are designed to address the manufacturing community, which represents significant added value for us.” A supply consignment is shipped to Hennecke every Wednesday via the Köln-Rath branch. Flexible deliveries are also made as required. Initial contact with the management at Hennecke was made through branch manager Niels Jablonski and Key Account Manager Roelof Wittler. Joint meetings were held on site and tenders were prepared in cooperation with the colleagues from the Engineering department. Today, Niels Jablonski is the primary contact partner for Hennecke GmbH. HANSA‑FLEX provided address books containing the details of all its branches for those employees with international responsibilities. In this way, all Hennecke employees always have the address of the nearest HANSA‑FLEX branch ready to hand and if necessary they can buy items simply by quoting the Hennecke customer number. Flexible, professional, reliable. Attributes that describe both our companies.
Learn more
- 12.03.2024
Efficient hose management
GKN benefits from seamless interaction between company and service providerFind out more - 12.03.2024
Close proximity, short response times
BSH Hausgeräte benefits from the full-service offerFind out more - 12.03.2024
Keeping the world in motion
Just a stone’s throw away from Hamburg airport is a city within the city – the head office of Lufthansa Technik AG. HANSA-FLEX supplies a large number of products, including several that are incorporated into the test benches.Find out more