HANSA-FLEX is a partner of Stadler Deutschland GmbH in the integration of air-conditioning lines in the first air-conditioned S-Bahn trains for the Berlin/Brandenburg region.
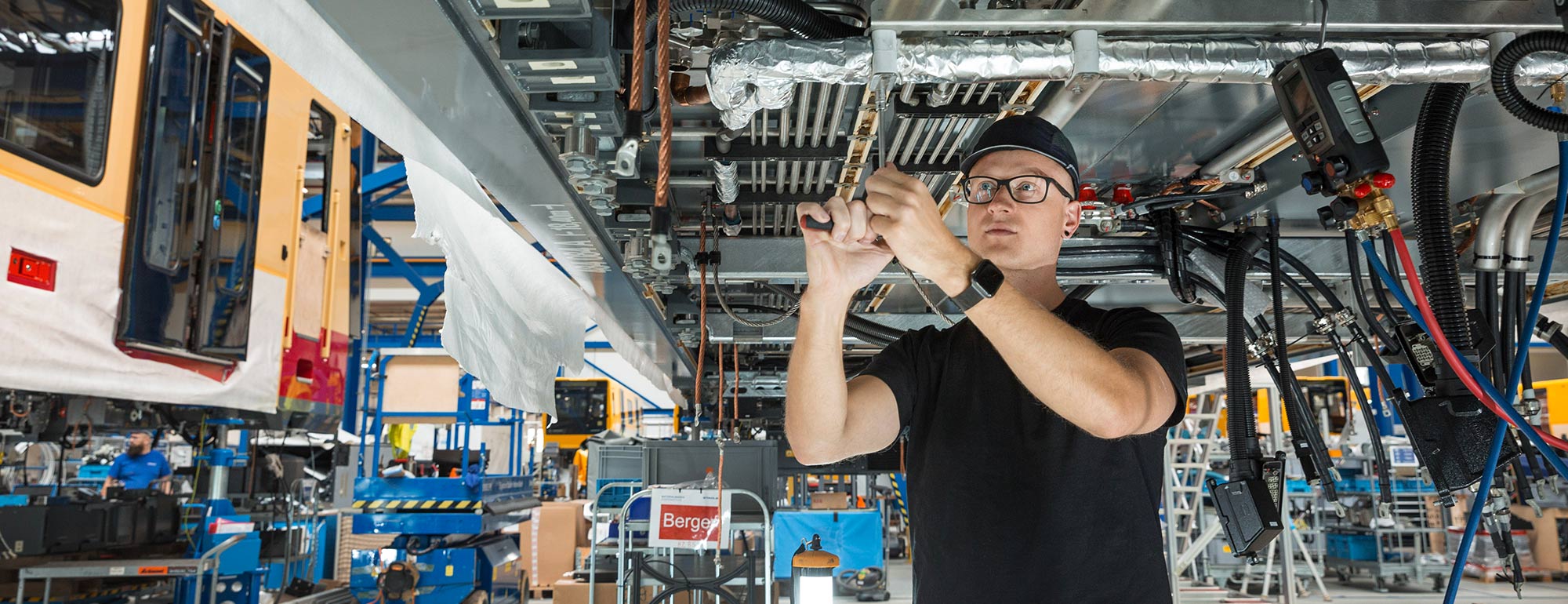
28.08.2023
First air-conditioned S-bahn trains in Berlin
HANSA‑FLEX AG and the rail vehicle manufacturer Stadler Deutschland GmbH have been working together for around 20 years. The two companies have now successfully strengthened their cooperation with the integration of an air-conditioning system for Berlin’s new suburban railway.
HANSA‑FLEX and Stadler have enjoyed a long-standing partnership. For example, HANSA‑FLEX and Stadler have already developed, among other things, a stainless-steel piping assembly for the pneumatic braking system in the underfloor area of rail vehicles. “This saves the fitters at Stadler an enormous amount of time, as they don’t need to attach each pipe individually. This assembly is now installed in almost every project, and HANSA‑FLEX supplies several hundred of these units every year,” reports Paul Sielaff, Area Sales Manager Berlin / Brandenburg at HANSA‑FLEX. The contract for Berlin’s new suburban railway was a special challenge, in that for the first time ever, the passenger compartments were to be air-conditioned. This may sound quite simple, but it was in fact a tricky challenge.
Especially complex piping
The tunnels in Berlin are fairly low, and it is difficult to install air conditioning units on the roofs of rail vehicles. Stadler therefore designed a split air-conditioning system which is compactly integrated inside the vehicle as well as underneath it. “This results in very sophisticated refrigerant piping with tight bending radii, running partly under the floor and partly in the interior ceiling, so that everything is as inconspicuous as possible,” explains Nicklas Meyer, Technical Project Manager for the Berlin suburban railway project at Stadler. As HANSA‑FLEX was familiar with Stadler’s rail vehicles, the system provider was brought on board to accompany the new project from conception to commissioning. The task was not only to supply the relevant components, but also to assemble the pipelines, test them in accordance with the strict guidelines of Deutsche Bahn and finally fill them. Air-conditioning technology was previously uncharted territory for HANSA‑FLEX. “We approached this task with a lot of respect, but I knew that I could rely on our HANSA‑FLEX experts, so I was able to commit to it with total confidence,” recalls Sielaff.
Due to the good cooperation in the field of pneumatics, it was our wish to win a competent partner like HANSA‑FLEX for this project. We appreciate the willingness to perform with which HANSA‑FLEX responds to customers.
Nicklas Meyer
Technical Project Manager Stadler
Air conditioning technology requires special expertise
Refrigerant piping consists of copper pipelines that have to be brazed on site at the vehicle. “Supplying the pipelines from Dresden Weixdorf was no problem at all,” comments Sielaff, adding: “But not every fitter is qualified to do soldering on a train. Because of the very high leak-proofing requirements, specially qualified people are needed for the installation work.” Andreas Fano (Operations Manager Berlin) and Paul Sielaff accordingly put together a team of technicians for this demanding task and provided them with the necessary training. Air-conditioning technology in this form was breaking new ground for HANSA‑FLEX, and Paul Sielaff as well as the team at the Hennigsdorf branch welcomed the task. “It is part of our corporate philosophy that, as a system partner, we focus on the needs of our customers. And if that means creating a new business unit out of nothing for a good, long-standing customer like Stadler, then that’s what we do,” stresses Sielaff. Stadler Germany appreciates this can-do attitude: “Due to our positive cooperation in the field of pneumatics, it was important to us to acquire a competent partner like HANSA‑FLEX for this project. We appreciate the commitment with which HANSA‑FLEX responds to customer requirements,” explains Nicklas Meyer.
Extending air-conditioning expertise
As work had to be done directly on the vehicles, 14 HANSA‑FLEX fitters were regularly on site at the Stadler works. A remarkable achievement, considering that everything was developed from within the branch. Paul Sielaff and Nicklas Meyer confirm the excellent cooperation and coordination between colleagues. Six years after the initial tender, the project is now slowly coming to an end. From development to the finished vehicle, HANSA‑FLEX accompanied the construction of a total of 85 four-car and 21 two-car suburban trains. The newly acquired expertise will, of course, remain with the company. At the moment HANSA‑FLEX is setting up a designated air-conditioning team, which from now on will also be able to take care of air-conditioning systems on behalf of other customers, from the initial consultancy to the finished installation. Together with Stadler HANSA‑FLEX is already working on further environmentally friendly solutions for future projects.
.
Learn more
- 12.03.2024
Efficient hose management
GKN benefits from seamless interaction between company and service providerFind out more - 12.03.2024
Keeping the world in motion
Just a stone’s throw away from Hamburg airport is a city within the city – the head office of Lufthansa Technik AG. HANSA-FLEX supplies a large number of products, including several that are incorporated into the test benches.Find out more