BSH Hausgeräte benefits from the full-service offer
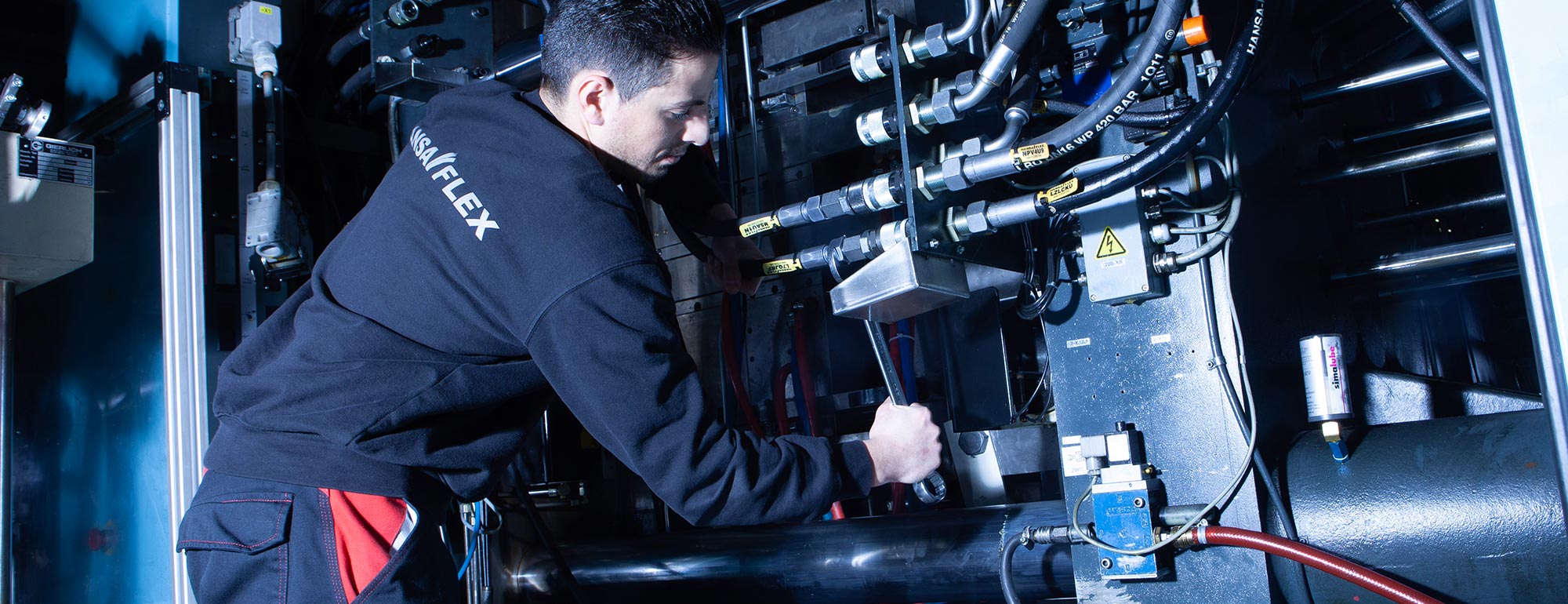
04.03.2015
Close proximity, short response times
Whether industrial, fluid or 24-hour services, all HANSA‑FLEX services are characterised by outstanding reliability, rapid speed and great proximity. And for the BSH Hausgeräte GmbH vacuum cleaner plant in Bad Neustadt, this proximity is even greater than ever – for a simple reason: the plant and the local HANSA‑FLEX branch are direct neighbours.
Alexander Cilluffo is a field sales technician at the HANSA‑FLEX branch in Bad Neustadt. If he or anyone else from his team under workshop manager Sascha Diemar is called for a service job, the modern, fully equipped service vehicles are used. When assisting BSH Hausgeräte GmbH, however, the use of a vehicle is often not necessary. This is because the two companies are neighbours. Germany’s largest vacuum cleaner plant has been owned by BSH since 1996 and has to face global competition every single day. The company therefore uses the latest production processes for the world-famous vacuum cleaner fans and high-precision, multi-component, large plastic parts. In this environment, downtime is business critical, making reliable service extremely important.
A sought-after one-stop partner
This particularly applies to the maintenance of the hydraulic components used in the production process. Eight toolmakers, four fitters and four electricians are responsible for servicing at BSH. Their area of responsibility includes 28 injection moulding machines that are used to produce plastic housing components weighing up to 1,000 grams. The hydraulics in the plastic machines work at a maximum operating pressure of 170 bar. “Process-reliable systems and machines are critical to our production processes. We are pleased to have a professional system partner who can offer complete hydraulic services right next door in the form of HANSA‑FLEX”, explains Marco Geis, head of servicing at BSH.
“Our production stands and falls with process-reliable systems and machines. We are glad to have HANSA‑FLEX as a competent system partner in our direct neighbourhood, offering a complete hydraulics service.”
Marco Geis
Head of Maintenance at BSH
Efficient material logistics
The opening of the Bad Neustadt site in 2008 brought about new customer service opportunities. The proximity enabled even faster services. In most cases, BSH now no longer needs its own warehouse for spare parts such as hoses, screw fittings, seals, valves and consumable materials. The company has therefore reduced its warehousing costs while retaining the same optimum supply level because HANSA‑FLEX constantly keeps all parts in stock. The HANSA‑FLEX X-CODE makes ordering and the spare parts procurement process far simpler. The alphanumeric code identifies all product features of hydraulic connection elements – as precisely as a fingerprint. “This eliminates the possibility of misunderstandings. Spare parts are always available to us quickly and the hose lines can be assembled without any time-consuming queries”, reports Geis from experience.
Added value through service
Like all other sites, HANSA‑FLEX Bad Neustadt has tailored its range of products and services to customer requirements. “We naturally also cover the whole range of products and services in Bad Neustadt but we also specialise in injection moulding”, explains Cilluffo.
This is something that BSH particularly values: “The fluid service and industrial service divisions play a major role in safeguarding system availability in our production facilities”, comments Geis. For example, the fluid service division ensures effective oil servicing in order to reliably prevent excessive component wear and thus disruptions and even production downtime. The hydraulic specialists in the industrial service division are responsible for inspecting, maintaining and servicing machines on site in the plant. HANSA‑FLEX can even provide optimisation services and completely refurbish production systems.
24-hour service
The branch also offers the popular mobile rapid hydraulic service for emergencies. If on-site assistance is required, a customer service employee with a fully equipped workshop vehicle can be contacted around the clock. Hoses are assembled and repairs conducted in the service vehicle itself to keep downtime to a minimum.
A tried-and-tested system partnership
One factor that is particularly well received by BSH is that HANSA‑FLEX provides not only components and services but also professional advice about all hydraulics-related matters: “Even in the field of fluid technology, we sometimes come across tricky challenges. We have specialist contacts in the HANSA‑FLEX branch for all questions. The urgent jobs that we often receive in production can therefore be carried out”, states Geis in praise of the work of the neighbouring hydraulics specialist.
Profile: BSH Hausgeräte GmbH
BSH Hausgeräte GmbH is the largest manufacturer of household appliances in Europe. In 2013, the company generated sales of around 10.5 billion euros. The Group has 42 production sites in 13 countries in Europe, the USA, Latin America and Asia. BSH employs around 50,000 people worldwide.
Learn more
- 12.03.2024
Silent night, busy night
KKF Fels GmbH commissioned HANSA-FLEX to change the hose on an injection moulding machineFind out more - 12.03.2024
Non-stop operation
The self-discharging freight train of Havelländische Eisenbahn AGFind out more