The self-discharging freight train of Havelländische Eisenbahn AG
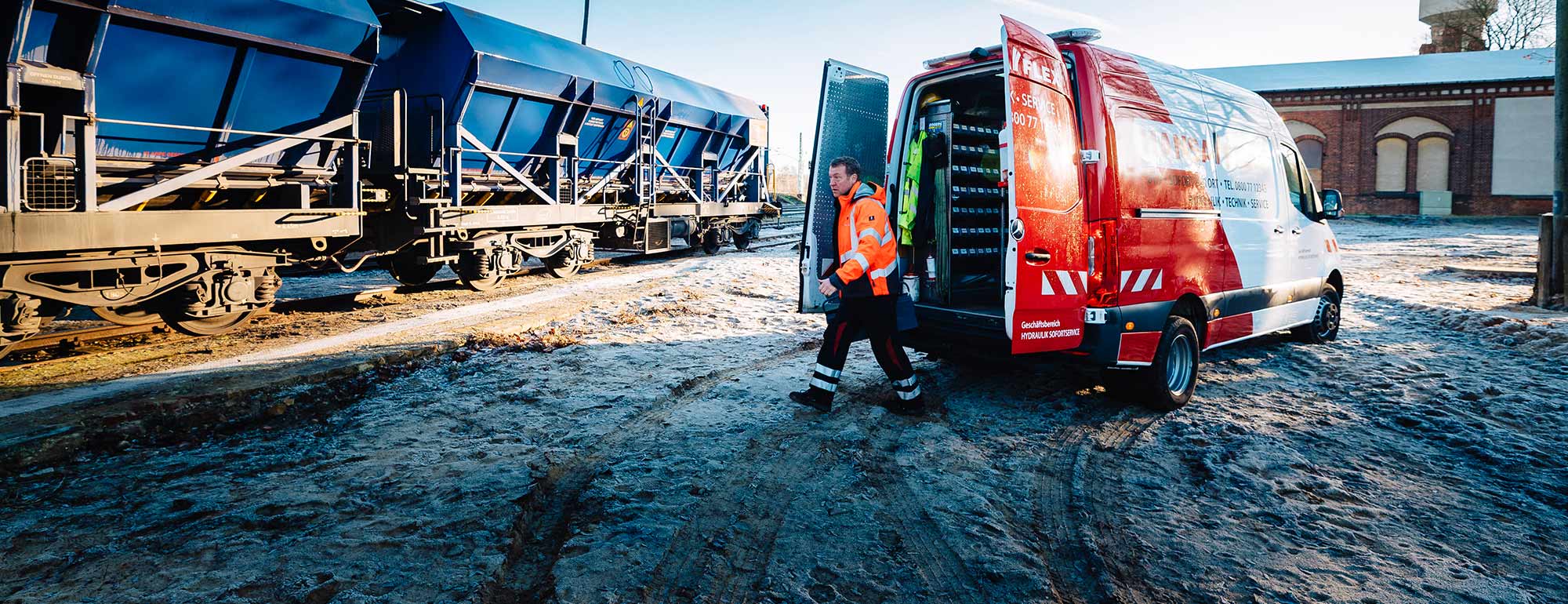
06.03.2022
Non-stop operation
The scene is a quarry in Saxony-Anhalt: wagon by wagon a freight train passes slowly under the filling station. The hoppers on the wagons are filled with bulk materials such as sand, gravel or grit. At first sight it looks like a normal freight train, but in fact it represents a very special piece of technology: the self-discharging freight train of Havelländische Eisenbahn AG (HVLE). Conveyor belts transport the freight efficiently and precisely to the unloading point. Everything is driven by a complex hydraulic system which is overseen by HANSA‑FLEX.
It takes six hours until the last wagon passes under the filling station and is loaded. The train now leaves for Hamburg, where the freight is expected at the Hansa Port facility. The journey takes a further six hours. “Whenever possible we travel at night to avoid passenger trains”, reports Steffen Meyer, Head of Fleet Management Freight Wagons at HVLE. Referred to in short as the “SSDT” (for Super Self Discharging Train), the train features impressive dimensions: with a length of 650 m and travelling at 40 km/h it takes over a minute for it to pass by. Almost 100 lorries would be needed to transport its 2,800 t load. But all these superlatives are nothing special compared to the technology used in the 46 wagons.
Unloading by conveyor belt
Hamburg, the SSDT’s destination. In the middle of the night the customer – a large dealer in building materials – no longer has any employees on the site. This is no problem, because in order to discharge its freight the train doesn’t need to travel via an unloading station, from where the cargo is subsequently transported to its final destination. The train can automatically unload bulk materials into a silo, storage yard or truck on any straight section of track. For this purpose the wagons are permanently coupled to form seven units with six wagons each, and one unit with four wagons. A conveyor belt runs under the hoppers along the entire length of each unit.
In order to start the discharging process, the three members of the HVLE unloading team close the gaps between the units by folding down conveyor belt bridges. This is carried out to a large extent automatically by remote control. Once the sections are closed the conveyor belts go into operation. When a hopper is opened, its cargo trickles through a hatch onto the belt and is transported to the middle of the train. This is where the discharge wagon is located. Its telescopic boom can be swivelled by 120 degrees and bridges the last metres to the destination with a conveyor belt. Around 750 t per hour can be discharged in this way – completely without any external power supply, as each unit has its own diesel generator for the hydraulic system. In order to serve another unloading location with a different type of bulk material, it is only necessary to move the discharge wagon a few metres further and open another hopper.
Mobile service around the clock
“This principle saves on manpower and shunting time,” says Steffen Meyer. And this is precisely why HVLE purchased the train especially for trips between Saxony-Anhalt and Hamburg. It was originally produced in Romania. Since the train could not be used to capacity there, it stood on a siding for several years. It was in a corresponding condition – especially with regard to the hydraulics. The seals were porous, the oil contaminated, valves were not working. “We worked with the manufacturers to get the train ready for operation again,” reports Meyer. But even when the train was put into service after several test runs, the hydraulics remained vulnerable to breakdown. Since the train is in operation 24 hours a day, six days a week, a flexible hydraulics partner was required. “HANSA‑FLEX provided us with very good support,” recalls Meyer. “Initially, the Industrial Service and the Rapid Hydraulic Service were in continuous operation”, adds Paul Sielaff from the HANSA‑FLEX Hennigsdorf branch. Routine applications were the exception rather than the rule, because in hydraulics there is nothing off the shelf. For example, even experts from the IHA (Internationale Hydraulik Akademie) were sometimes called upon during the troubleshooting. “We maintain excellent and active communication with our hydraulics partner in order to achieve the best possible results and use the train continuously,” confirms Meyer.
Diagnosis by the Fluidservice
Hamburg: after six hours the train has been completely unloaded. When the customer’s employees start their shift in the morning, the stocks of material have been replenished. It is these short turnaround times in which minor repairs can be carried out. To speed things up HANSA‑FLEX has marked all hoses with the X-CODE, so that spares can be produced in advance.
To the present day fast repair jobs are still required, because all the train’s hydraulic components are subject to extreme stresses. “The mixture of dust, sand, gravel and water is poison for the hydraulics,” says Meyer. This is why HVLE stocks hydraulic cylinders individually manufactured by HANSA‑FLEX. It enables the soiled actuators to be regularly taken to the branch in Hennigsdorf for maintenance.
The Fluidservice team also plays a key role in the maintenance of the train. They can operate directly by the railway line, complete with washing equipment, a mobile laboratory and fully fitted workshop. Oil analyses not only show when there is so much dust in the pipes that an oil change is necessary. They also provide information about malfunctions and excessive wear, for example when the experts detect brass in the fluid. Around 400 litres of oil flow through the hydraulic system of each unit and the discharge wagon. During a complete oil change, nine tanks have to be cleaned and 3,200 l of oil forced through the pipes.
The empty train now begins its journey back to Saxony-Anhalt. There it is loaded once more and a new 24-hour shift begins.
Learn more
- 12.03.2024
Keeping the world in motion
Just a stone’s throw away from Hamburg airport is a city within the city – the head office of Lufthansa Technik AG. HANSA-FLEX supplies a large number of products, including several that are incorporated into the test benches.Find out more - 12.03.2024
Silent night, busy night
KKF Fels GmbH commissioned HANSA-FLEX to change the hose on an injection moulding machineFind out more - 12.03.2024
Close proximity, short response times
BSH Hausgeräte benefits from the full-service offerFind out more